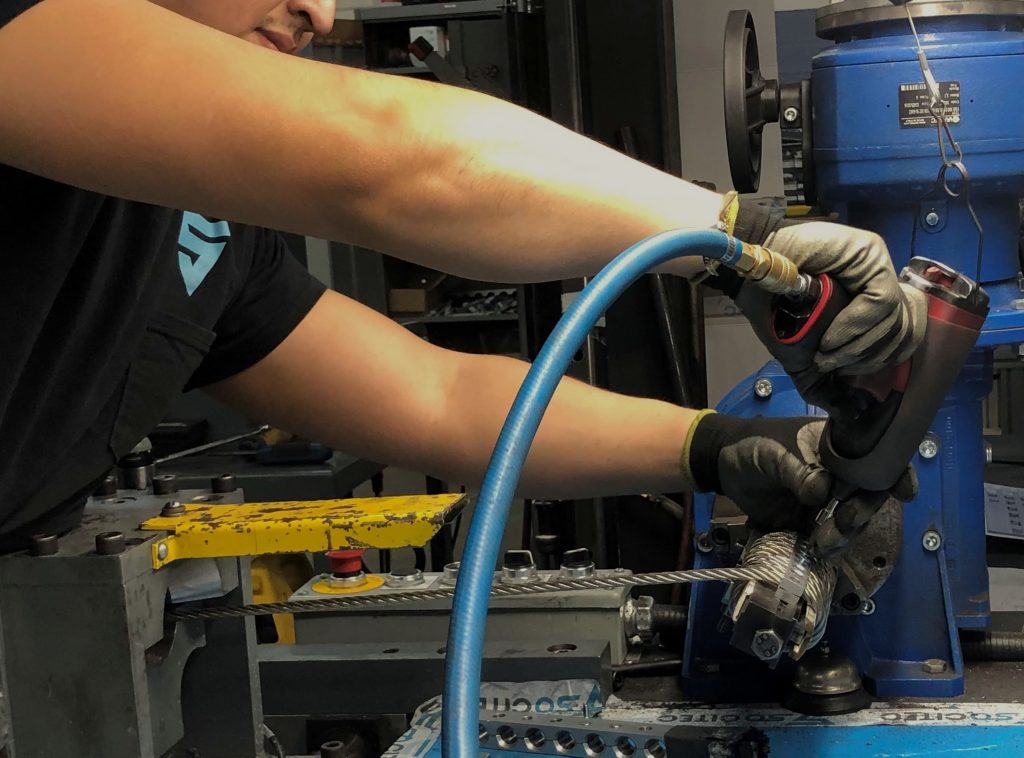
Expanded Production for Better Lead Times
02/17/2020
As a part of the Socitec Group, Socitec US has established itself as a global leader specializing in vibration isolation and shock control systems on a global scale. Socitec’s success is the result of a collaborative approach that integrates advanced technologies with 50 years of industry expertise, enabling us to deliver effective solutions even in the most challenging environments.
To develop effective solutions for shock and vibration challenges, it’s crucial to analyze and comprehend the entire dynamic system. This system consists of various factors, including the equipment that needs isolation, the environmental conditions, the input forces, and the response characteristics of the isolators.
At the core of the Socitec Group’s approach to shock and vibration isolation is an engineered methodology that is tailored to meet each application’s unique requirements. This method has been a guiding principle for Socitec since it first started and has evolved into an advanced process that incorporates cutting-edge modeling and analytical software along with the most rigorous quality control procedures. With our vast experience in numerous applications and a broad range of products available, we are confident to offer effective solutions for any shock and vibration challenge.
At Socitec, we collaborate with our customers to understand their specific needs and requirements. By doing so, we can design and produce custom solutions that are effective and efficient for their specific application.
We utilize a variety of resources such as n-Degree Of Freedom SYMOS Simulation, Advanced FEA, 2D/3D CAD, and Physical Testing Services. These resources enable us to accurately model and simulate the behavior of mechanical systems in response to shock and vibration, as well as to test and validate the performance of our solutions in a real-world environment.
These efforts enable us to provide comprehensive reports that document the features of our isolators and the responses of system components, providing unparalleled insights for every application.
Our markets include industrial, manufacturing, defense, aerospace, and more. We possess expertise in the design and application of wire rope, elastomer, and coil spring based isolation.
PARIS
CHICAGO
BERLIN
LONDON
SHANGHAI
With more than 100 years of combined experience, the merger of Vibro / Dynamics and Socitec creates a global presence in the US, Europe and China.
02/17/2020
06/30/2021